While
architects strive to deliver great buildings, technical services manager
Steve Cleminson at single-ply roofing specialists SIG Design & Technology
explores how bringing in experts from the outset can avoid compromising the
vision down the line. |
Architects have a hard balancing act to maintain. Clients expecting a king’s
banquet on a pauper’s budget. Problematic sites and locations prove
difficult to design into. There’s complicated and, often, conflicting
government legislation to work around while bureaucrats are lining up to
pull plans apart. All of these create extra hurdles while trying to deliver
buildings that perform on aesthetics, functionality and commerciality.
|
Not
surprising, then, a building’s details are often the key to its success.
|
But if
architects have to focus on balancing the overall picture and the devil is
in the detail, getting the most out of a project relies on working with
trusted, specialist partners who can help to design problems out of each
element. |
At SIG
Design & Technology, we wouldn’t expect to come to a project and not add
value in this way. We spend our lives focussing on a single aspect of a
building and so we should be able to help to resolve issues, improve
solutions and make the roof work much harder on any project. |
Roof falls are a case in point. While British
Standards stipulate that all single-ply roofs should achieve a fall of 1 in
80, it is often over looked that this recommendation is for an “achieved”
fall and the standard goes on to say that in order to actually achieve this
pitch we should be designing at a minimum of 1 in 40. |
There
are so many good common sense and technical reasons for working to the good
practice code rather than the bare minimum on falls but more often than not
the minimum standard is specified or at best a halfway house of 1 in 60.
|
Your main
objective with any roof should be to get the water off as quickly as
possible. Ultimately, you’re not designing a swimming pool, so while roof
membranes will withstand torrents, water ponding can lead to the roof
failing. It’s not the water itself that can lead to accelerated aging of
roof coverings, but rather the build up of leaf litter, moss, fungus and
algae growth. |
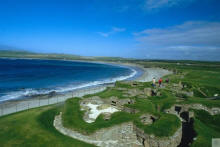 |
Also
poorly drained roofs can lead to greater imposed loadings, increased levels
of water ingress if the coverings are damaged, problems of icing during
winter and the associated slip hazards during maintenance inspections.
|
Then,
there are the building tolerances to take into consideration. |
Designing at 1 in 60, even, is all very well as long as your building
tolerances are perfect. But buildings are never 100 per cent perfect.
Factoring in this inevitability will avoid problems further down the line. |
Our
membranes are designed to last for up to 40 years as long as they are
installed in line with good practice and are looked after. Getting the most
out of a membrane depends on the design and build being right from the
outset and also ensuring that the recommendations regarding the periodic
maintenance are adhered to. |
Our star single-ply membrane, Rhepanol fk has
been installed on some 90 million sq m worldwide over the last 50 years.
|
It’s
been hailed as the world’s most advanced single-ply roofing membrane and
it’s also the oldest. First developed in 1938, it has been adapted since to
provide the architect with much greater flexibility, introducing options for
green and photovoltaic roofs. |
Based on
polyisobutylene (PIB), it is the only single-ply membrane with the unique
independent Life Cycle Assessment rating of DIN EN ISO 14040 part ff. It has
a unique self-sealing edge and Gripfix system, so it can be installed
quickly and with minimum fuss in three simple steps. The self-sealing edge
forms an impermeable seam. There are no naked flames, installation is quick
and simple, in no small part due to the factory produced self-sealing edge
and preformed detailing accessories. And as the membrane is compatible with
bitumen, it can be laid over almost any substrate which is structurally
sound. |
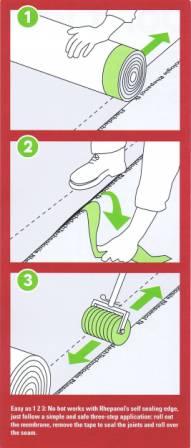 |
But even with
these credentials, durability is only as good as the design and
installation. |
Sure, you can
drive a Ferrari at 90mph in first gear but you wouldn’t expect the dealer to
pick up the tab when the engine blew up. |
I understand the
commercial pressure of value engineering a project. Architects are under
increasing pressure to shave money off build costs. The first place to look
is specification – but decisions do have implications so you have to make
sure they are the right ones. |
The best way to
make sure you aren’t cutting corners in the wrong areas is to seek expert
guidance and ask the manufacturer/supplier partner to look at where you can
cut costs without designing in problems. |
I much
prefer to spend my time working together with architects to get things right
at the beginning, even when there’s no immediate commercial gain, than
trying to reach a compromise between the material requirements and the
signed-off design. |
It
makes sound sense to bring a specialist in to design within the parameters
of your overall vision. Not only will they research the products but they
will also provide a design complete with calculations of U values,
condensation risk analysis, acoustic performance and wind uplift
calculations. Together, these not only combine compatible materials within
the build up but also ensure interfaces are correctly designed with other
building elements. |
I come
across a lot of projects where the main reason for not delivering best
practice on falls is down to cost. Yet here again is an example of how by
working with specialists you can find budget busting ways to achieve the
ideal. |
Commonly, roof falls are or can be achieved through the use of tapered
insulation; this can be in the form of multiple layer build ups or even
pre-bonded boards. However on large projects, where insulation thicknesses
can become excessive, the use of screed to falls, firings or a slight
alteration to the structural elements can deliver more effective and less
costly ways of delivering the fall. |
Falls
are not the only topic in a whole matrix of things to think about. We often
need to deal with issues around how the falls interact with the rest of the
roof geography or other building elements – the parapet, windows, doors, or
rooflights, for example. |
We’ve
had cases where on a refurbishment project the best way to achieve the
required falls was to recommend the removal of a run of existing ribbon
windows and replace these with shorter ones to allow a tapered scheme to be
installed whilst still achieving the minimum 150 mm recommended upstand
height at this interface. |
The
client in this instance wasn’t just interested in a meaningless “scrap of
paper warranty”, he wanted a sound solution that complied with good practice
and he acknowledged that to ensure the life expectancy of the coverings he
needed to abide by the rules, common sense and good advice based on years of
experience. |
Location and building usage will also dictate the choice of materials used
and sometimes there has to be a play-off between the two. It doesn’t always
follow that where a material worked on one job, the same solution is
suitable for the next. |
For
example, bonded membranes may be inappropriate for coastal areas because of
the excessive wind uplift. This said, we wouldn’t normally recommend
mechanical fixings over something like a swimming pool, because in a
building of high temperature and high humidity, penetrating the vapour
barrier may lead to condensation problems. This aggressive environment may
also highlight / exacerbate problems of bimetallic corrosion between the
metal deck, the structural elements and the metal fixings. So perhaps a
combined approach of bonding and ballasting may be a more risk reduced, cost
effective option, or even a green roof? Each and every installation needs to
be analysed individually. There isn’t always a one-size-fits-all solution. |
Whether it’s a 70sqm London townhouse or a Scottish ancient monument, we
will always take the same approach: we will identify the criteria that will
impact on design, hone them down to a sensible number of solutions so we can
design it right, install it right and achieve the best solution for the
building, project, location, client and end user. |
For
further information on SIG Design & Technology see
www.roofinfo.co.uk/sigdt |
|